As the logistics industry adapts and evolves to embrace new technologies, the need to test and improve solutions in real time has become more important than ever.
Linfox Chief Information Officer, Nick Delija explains, “our approach to innovation is to keep things simple to start with.
“We work collectively with our operators. We take their feedback on board and turn around enhancements quickly.
“We have created an incredibly efficient system that can be implemented time and time again to provide rapid solutions for customers.”
Working smarter in warehousing
This innovation-centred mindset has driven smarter solutions for warehouse setup.
Linfox’s Digital Warehousing Solution has been developed to significantly streamline processes and reduce the time and cost of site deployment and customer onboarding by creating an accelerated and reuseable warehouse template.
It has been developed with a deep understanding of the efficiencies customers are seeking, in particular reducing the time and cost for set up.
The key is understanding, configuring and standardising what the perfect warehouse looks like.
“We have created an incredibly efficient system that can be implemented time and time again to provide rapid solutions for customers,” said Nick.
A dynamic market landscape has seen supply chain organisations looking to define their point of difference.
Increasingly, the industry is seeking to build specialist expertise that isn’t necessarily part of the traditional approach to logistics.
“Having strong partnerships with SAP, Blue Yonder, Telstra, Microsoft, Swisslog and Snowflake to name a few, enables us to stay close to the latest innovation opportunities and work smarter across our business,” said Nick.
“The industry is demanding out-of-the box thinking that can only be generated in collaboration with other innovators.”
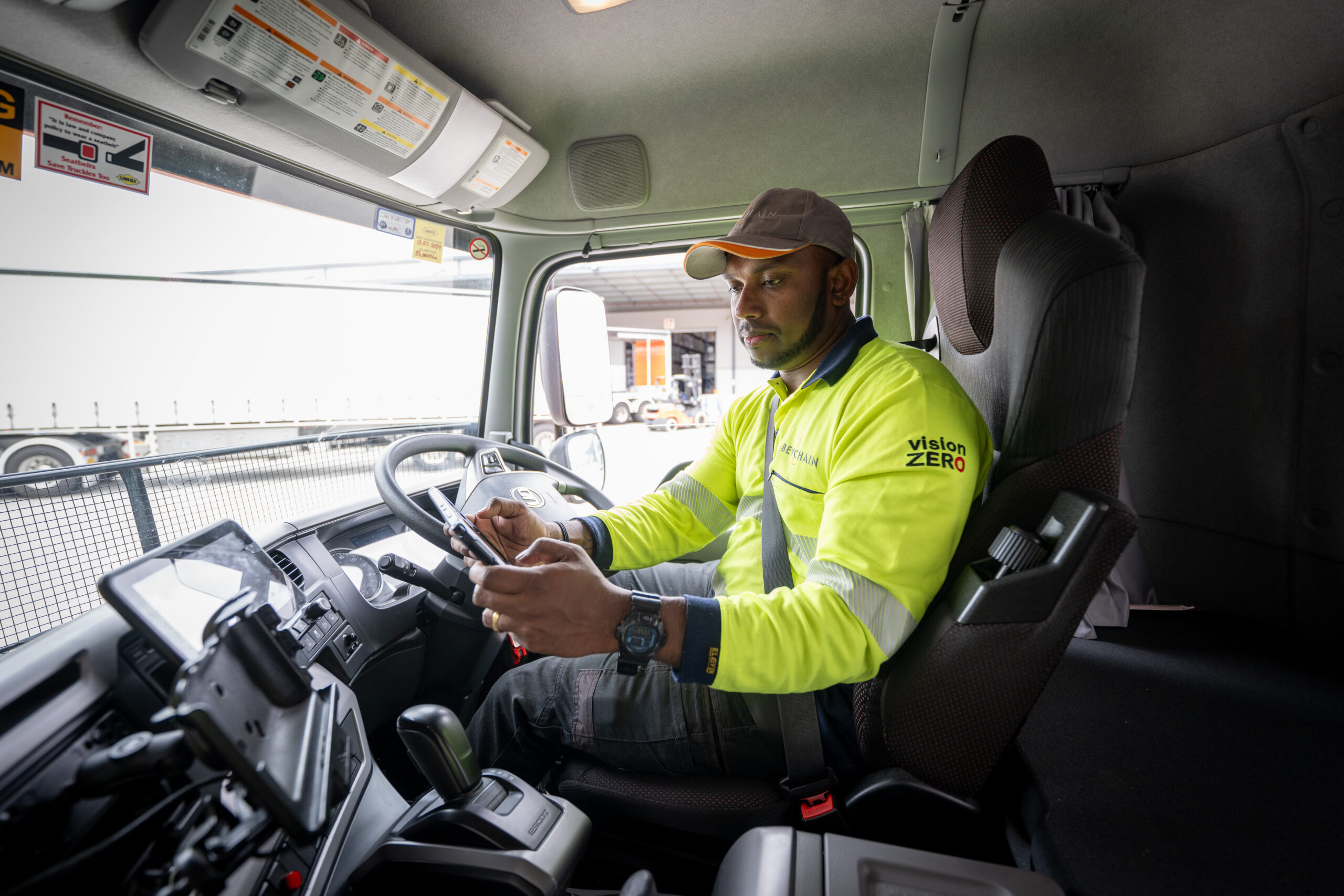
Driving digital innovation on the road
A new digital e-Runsheet solution is streamlining business on the road in a process inspired and informed by the drivers who do the work every day.
The FoxTrax driver paperwork digitisation initiative has resulted in a robust digital solution that seamlessly integrates with existing software and is capable of meeting Linfox’s diverse transport requirements.
Following a three-month trial of user testing with drivers, Linfox sites at Woolworths, Laverton and Dulux, Dandenong in Victoria have now fully transitioned from paper to electronic runsheets using existing FoxTrax driver tablets.
Linfox Executive General Manager Woolworths, Matt Sheridan explained: “Digitising operational processes significantly reduces manual data entry and paper administration, enabling our business to work smarter and act sustainably.
“The active involvement of our operational teams and drivers enabled us to learn a lot about the functionality of the system in real time and how it would impact our drivers.”
Reports from the trial period highlight positive adoption from both a user and a technical perspective, with a 77 per cent positive driver satisfaction rating and 100 per cent of trial participants opting to continue using the e-Runsheet solution daily.
“We have measured no loss in productivity thanks to the way we have engaged our drivers in the process.
“Simplifying and integrating a driver’s digital experience is key to adoption success,” said Matt.
Digital transformation, data analytics, and automation are shaping the future of the logistics industry and Nick explains the capability to bring quick solutions to market is integral.
“We always look for the best fit when thinking about how to solve our current challenges,” said Nick.
“These solutions have enabled us to focus on more value-add activities that make a difference to our customers.”
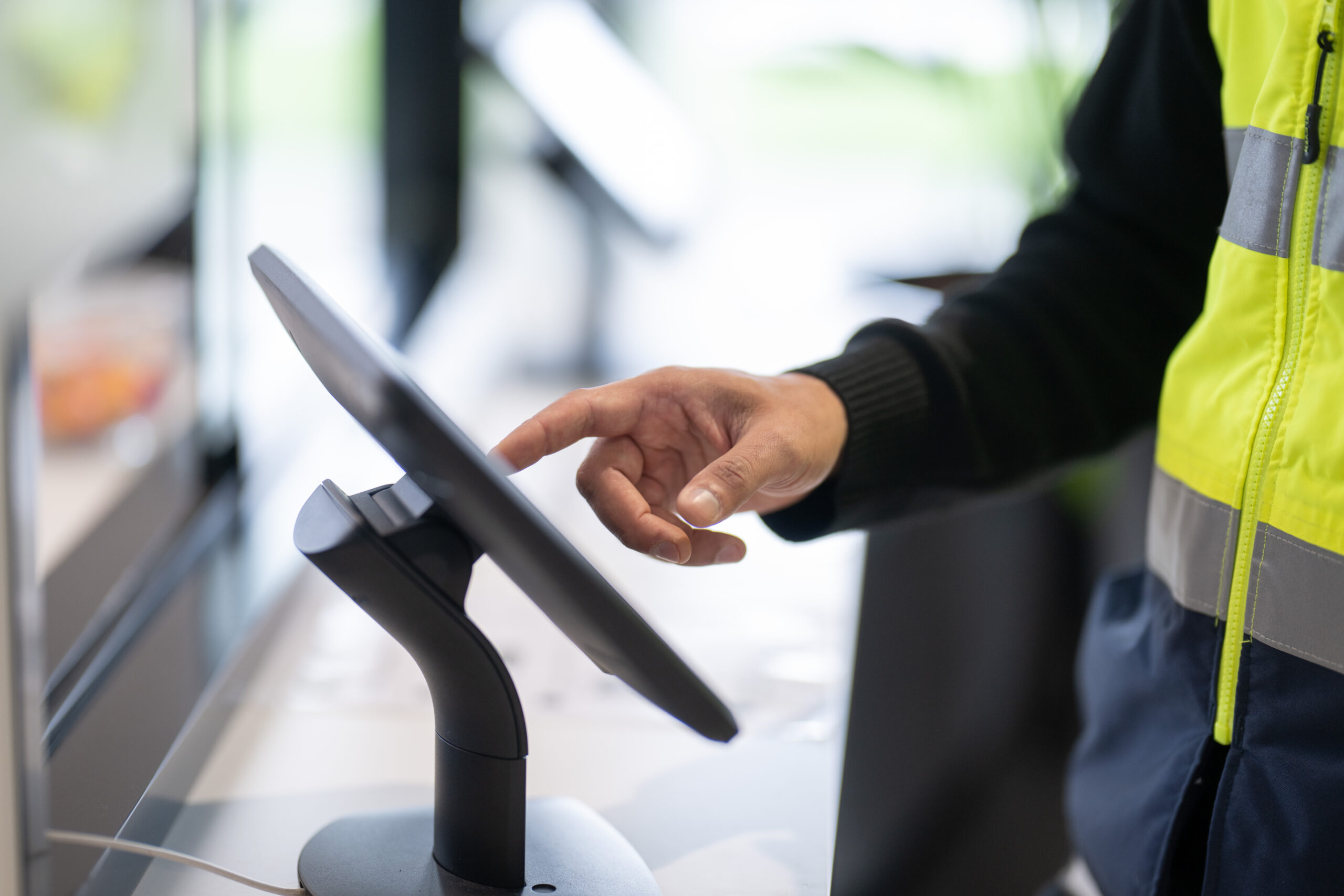
Sustainable innovation in New Zealand
In an organisation that has been founded on a pioneering spirit of continuous improvement, creative thinking and teamwork has also led to important ingenuity in tobacco packaging.
Linfox worked together with customers Philip Morris International (PMI) and Imperial Brands Australasia (IBA) in New Zealand to find smarter and more sustainable solutions to everyday challenges.
The goal was to replace existing heat tunnel machinery in warehouses to secure and ship tobacco parcels across the New Zealand network, which use large quantities of plastic to shrink wrap each parcel and emit high levels of heat and noise when in operation.
Working closely with PMI and IBA, frontline team members trialled and rolled out an alternative void tape solution; a tamper-evident seal that enhances security by instantly providing evidence of unauthorised attempts to access packages.
“We have forecast multiple sustainability benefits of this new system including the avoidance of 16 tonnes of plastic going into landfill and a reduction of 290kW of electricity use each year,” explained Executive General Manager New Zealand, Rob Farrar.
“Critically, our quality security practices have been maintained for our customers, with no increase in incidents of parcels being compromised since making the switch.
“We have now implemented this void tape solution across all Tobacco sites in New Zealand and we look forward to the continued benefits it will provide for our customers.”